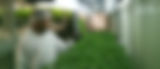
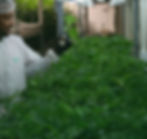
OUR OPERATIONS
Every MedCan product begins from a single source, our greenhouse in Isando, South Africa. Our state-of-the-art, fully indoor facility is purpose-built to cultivate flowers with absolute consistency and to meet the highest international standards.
All growth variables are precisely controlled and managed 24/7. We ensure that every step of our operation is transparent, rigorous, and dedicated to delivering the purest, most consistent, and most effective scientifically-grown medicine.
Most hydroponic cannabis cultivators typically use coco perlite or other inert media. At MedCan we prefer using a mix of coco perlite and a suite of rich organic amendments to support a robust and diverse microbiome while aiding the overall health and wellbeing of the plants.
This media is “the best of both worlds” as it has properties similar to that of true living/probiotic soils but also allows our cultivation team to have complete control of the mineral fertigation delivered to the plants while providing a well oxygenated root zone that encourages growth and vitality.
Our chosen media allow us to keep the plant free of soil borne pests and pathogens without using any chemical pesticides.
HIGH PERFORMANCE MEDIA
Arriving at our hero strains is quite a complex process. Our cultivation team starts off by planting hundreds of seeds in our ideally controlled indoor grow facility.
After close observation throughout their growth phases, they arrive at a shortlist of preferred phenotypes. They then take cuts from each of these to create Mother plants, and cultivate clones from the Mother.
Eventually they arrive at a single, hero, optimised phenotype from which the entire batch is grown.
PROPAGATION
PERFECTION
THROUGH SELECTION

TIME TO VEG
CULTIVATION
The vegetative (veg) process is a rapid growth phase in which focus is placed on growing and developing a robust and strong root network as well as vigorous and sturdy shoots and stems. This is the foundation from which high quality flowers are grown in later stages; and a good veg process is key to having a good flowering process.
In our vegging process, rooted cuts are grown under a minimum of 16 hours of light in a 24 hour cycle, to promote shoot and foliage growth. This prolonged exposure to light prevents the plants from flowering and allows the cultivators to develop the “structure” on which the flowers will grow.
FLOWER POWER
During the flowering stage the focus shifts to the production and nurturing of flowers. Light intervals are reduced to a maximum of 12 hours of light in a 24 hour cycle. This triggers the plants to stop vegetative growth (foliage and stems) and begin growth of reproductive tissue (flowers).
Cultivators encourage this by increasing the light intensity and the amount of nutrients the plants receive. Depending on the strain, this process usually takes between 56 to 70 days until the flowers are mature enough and contain the desired cannabinoids and terpenes at harvest. This stage of growth is much less rapid than the vegetative cycle, but the plants gain a drastic amount of weight as flowers swell and mature.
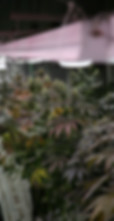
IDEAL HARVEST TIME
HARVEST
Once flower production has halted, the plants have fully developed capitate-stalked trichomes (the easily visible crystalline “hairs” that are abundant in terpenes and cannabinoids, including CBD and THC).
The Cultivation Team assesses the “ripeness” of the flowers by closely scrutinising the trichome heads to ensure the greatest concentration of phenolic compounds and cannabinoids are present in the trichomes (and the overall flower) at time of harvest.
At peak “ripeness” the plants are cut at the base of the stem and moved into a purpose built drying room in which they are hung upside down in the dark for a minimum of 14 days. The environment in the drying room is maintained at 16 degrees Celcius and 60% to 65% relative humidity to allow for a slow drying process that aids in the breakdown of non desirable phenolic compounds such as chlorophyll.

THE CURE'S IN THE CURING
POST-HARVEST
Once dry, the plants are bucked. They are then hand-trimmed to remove any leaves and non-flower matter. Once trimmed, the flowers are stored away to be cured until they are perfectly ready for medical use.
After curing, the final product is stored in airtight containers within a temperature controlled room where no light can enter. Final product is stored like this until packed and shipped.
Before any product is shipped, it is thoroughly analysed by third party independent laboratories to check whether flowers meet the very strictest requirements and quality standards. The exact amounts of THC, CBD and other cannabinoids are recorded in a unique Certificate of Analysis for each batch.

STERILE OPERATION
Full protective gear including full body coveralls, shoe covers, hairnets and gloves are worn in the facility at all times.
Shoes are sprayed with a liquid sanitiser aerosol before applying the shoe covers; and hands are washed and sanitised upon entry into the facility.
The comprehensive protection equipment prevents any possible cross-contamination that might occur.
STERILE OPERATION
Full protective gear including full body coveralls, shoe covers, hairnets and gloves are worn in the facility at all times.
Shoes are sprayed with a liquid sanitiser aerosol before applying the shoe covers; and hands are washed and sanitised upon entry into the facility.
The comprehensive protection equipment prevents any possible cross-contamination that might occur.